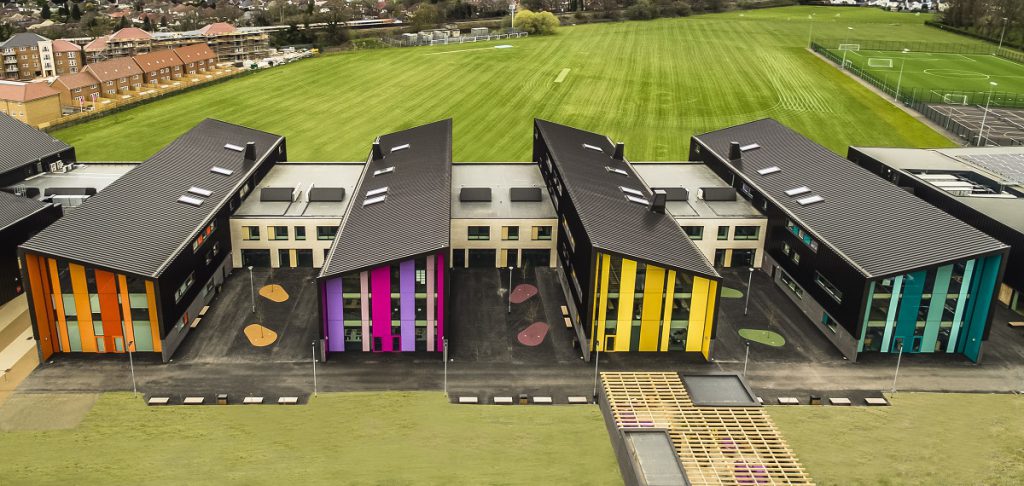
SIPS
Delivering a high-performance building system
Structural Insulated Panels (SIPs) are an advanced method of construction, exploiting composite panel techniques, and delivering excellent structural and thermal characteristics in one system.
The panels consist of an insulating foam core sandwiched between two structural facings, typically oriented strand board (OSB). SIPs are manufactured under factory-controlled conditions and can be fabricated to fit nearly any building design. The result is a lightweight building system that is extremely strong, energy-efficient and is quick to erect, and free from the complications of thermal bridging.
SIPs are engineered, load-carrying, timber-based panel products that can be used in walls and roofs of residential and light commercial buildings. These lightweight panels combine the structural and thermal envelope of the building; they are manufactured offsite in a factory and shipped to the construction site offering advantages to the build programme. This panelised form of construction allows SIPs to be assembled to form highly airtight, energy-efficient building envelopes.
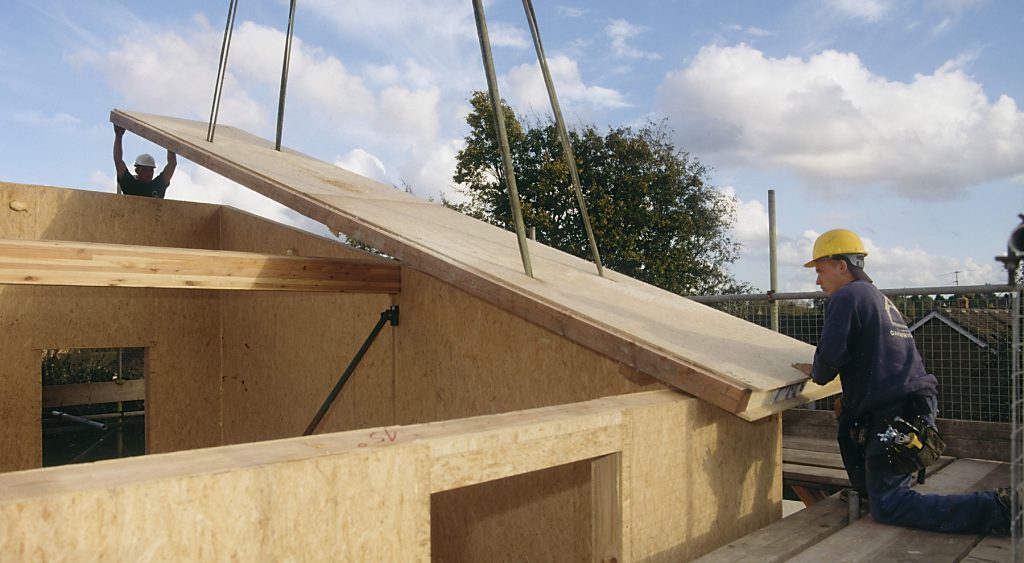
Why Choose SIPs?
- SIPs are manufactured to bespoke measurements and designs, reducing material waste
- Offsite manufacture gives cost and supply predictability
- High insulation performance results in lower building energy consumption, therefore, reducing CO2 emissions
- SIPs are suitable as roofing elements that maximise space for room-in-the-roof
- Quick installation on site allows for programme improvements
As a lightweight product, SIPs are often used on sites where ground conditions would make heavy building material un-economic.
Generally, SIPs are made by sandwiching a core of rigid foam insulation between two structural skins, though many different variations are included in the blanket definition. Typically, SIPs are commonly made using oriented strand board (OSB) as a facing material, with the most common insulating core materials being expanded polystyrene (EPS) or polyurethane foam (PUR).
During production, EPS is fully bonded with structural adhesive to the OSB skins whereas PUR is mainly foamed between the OSB skins, creating the bond. The core materials are responsible for providing thermal insulation, counteracting shear and transverse forces, and resisting moisture penetration. The insulating core also reduces the overall panel weight.
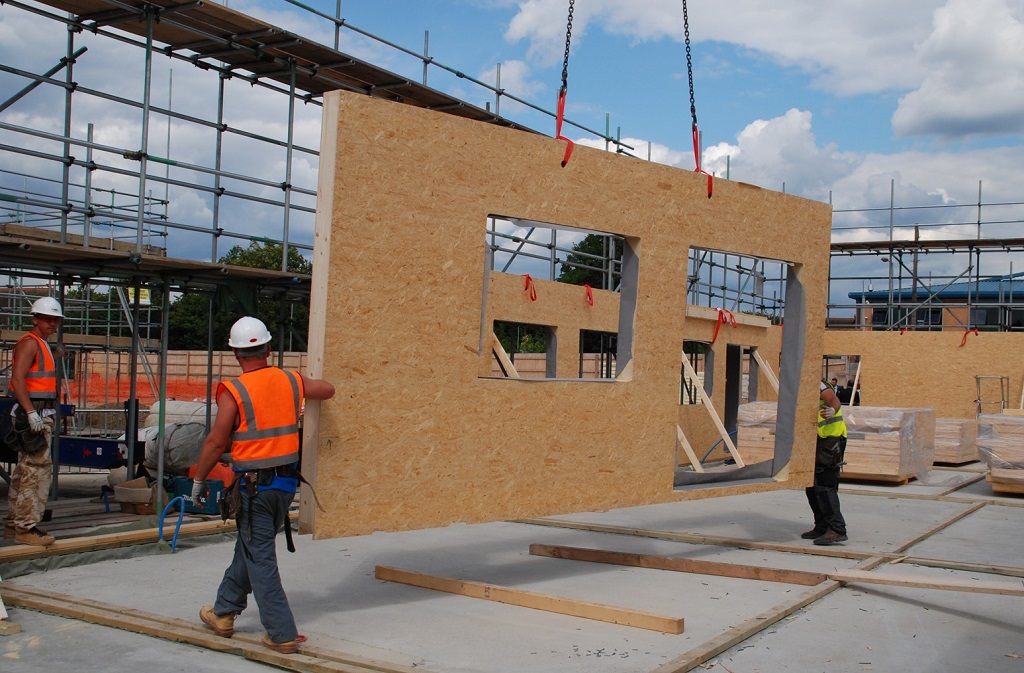