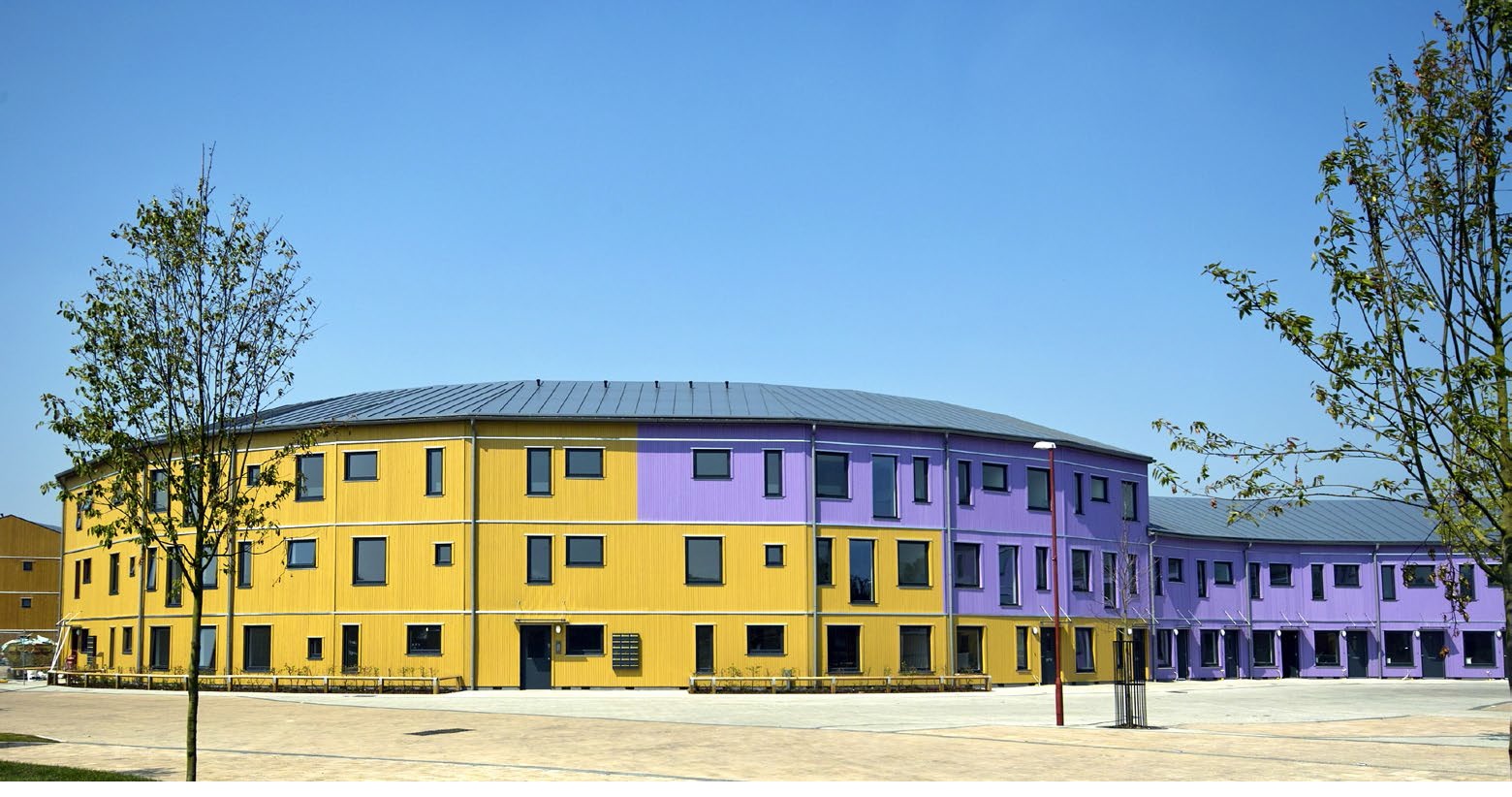
Project: The Serpentine, Aylesbury
Company: Stewart Milne Timber Systems
Sector: Residential
Technology: Timber Frame
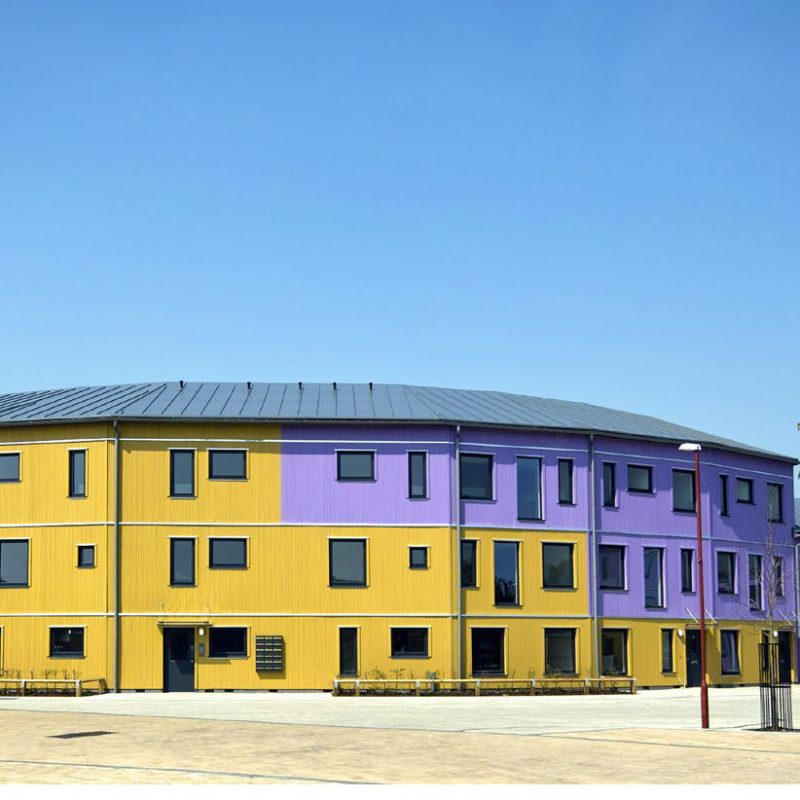
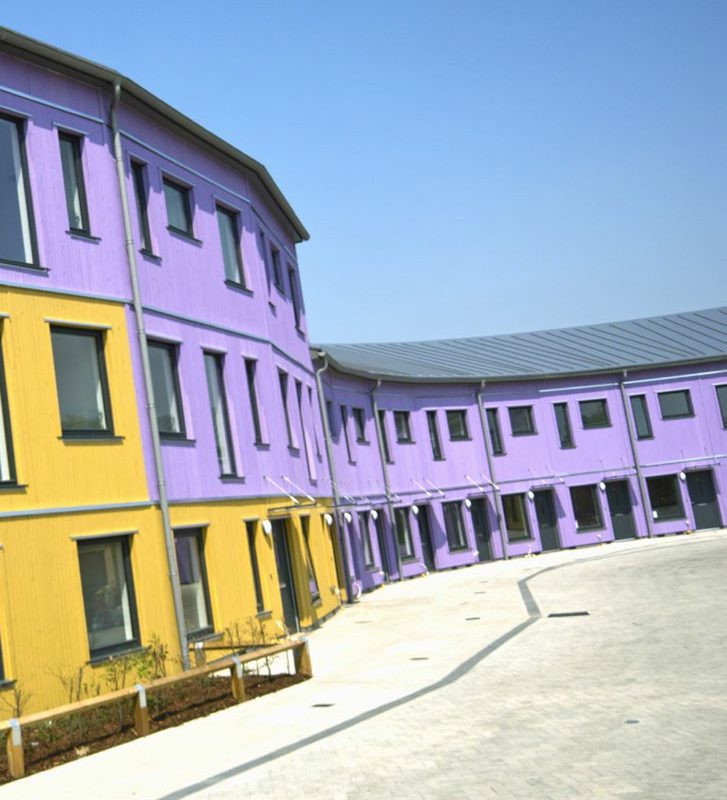
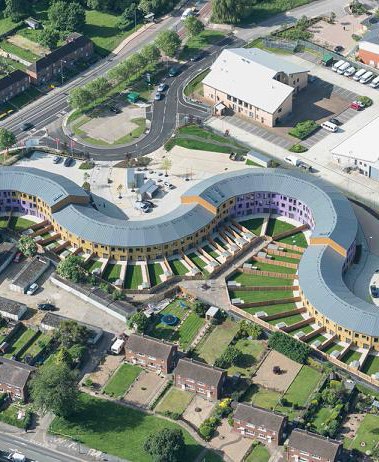
Overview:
In June 2012, Thames Valley Housing (TVH) welcomed the new residents of The Serpentine, its flagship affordable housing development in Aylesbury. Stewart Milne Timber Systems, the UK’s leading provider of timber system building solutions, played a crucial role in this innovative project, from the initial design through to the supply and erection of the closed panel timber build system. The success of this unusual design showcases both the flexibility and cost effectiveness of building with timber as well as the market leading expertise of Stewart Milne Timber Systems’ technical team.
Thames Valley Housing is a registered social landlord which provides affordable rented homes, shared ownership, market rent and accommodation for students and key workers in the south east of England. Its vision for The Serpentine was of a new kind of development; a genuinely sustainable community which will support the future of the town.
Project Type/Application:
The building divides the site into two clear zones: the ‘street side’ extends from the main entrance to the site and incorporates a child-friendly Home Zone, while the ‘garden side’ offers private green spaces for a range of the new homes and faces onto the residential area to the east. TVH was committed to using innovative materials and building methods to meet the highest standards of energy efficiency and sustainable living, while also challenging the architects to deliver a design with a very low build cost of less than £60,000 per home. Plus, with the housing association keen to hand over the keys to the new tenants, speed of build was a crucial driver. Compared with other traditional methods of construction, building with timber, and timber build systems in particular, is an incredibly flexible and cost effective means of delivering on these requirements in a short timescale.
Outcome/Results/Success Factor:
The experience and expertise of our technical and design teams was integral to the viability of The Serpentine, as we identified design and structural solutions which enabled us to meet the brief while keeping costs under control. For
example, the whole building is segmental, with straight walls, and in each house type all internal walls are set at right angles to one of the party walls. That allowed us to manufacture all of the floor and ceiling cassettes in our factory on our fully automated lines. Offsite manufacture and construction of the build system also delivered a further range of benefits for the client and future tenants that include: a factory quality product, produced and erected more efficiently, with few defects; greater air-tightness and better insulation which will result in lower energy costs in the future and help meet targets for sustainability; and a safer site throughout the construction period thanks to reduced manual handling.