
Project: Philip Oliver – Wayside
Company: MBC Timber Frame
Sector: Self Build
Technology: Timber frame
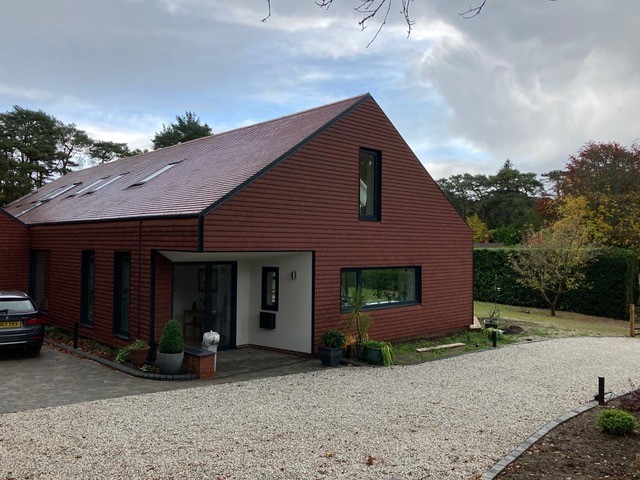

Back in pre COVID-19 days, in 2019, it was their daughter who brought their attention to a bungalow which, because of the potential for “single level” living, looked like it was a real candidate for a program of major change and improvement.
As is so often the case however, it was not long before it became clear that “the bungalow” was unlikely to survive an extensive program of alterations and improvements – demolition and a new self build would be both more cost effective in the long run, and far more likely to result in a thermally efficient home fit for the 2020s.
Importantly, their architect Craig Beech of Beech Architects offered sound advice that the couple should live in the bungalow for a year while they planned their new build.
Philip takes up the story, “Whatever home we were going to build, its orientation and position on the plot was going to be critical, we wanted from the outset to make the most of the available light and the best sight lines.
“We also knew that we wanted to source as much for the build as we could from the UK or, as second choice, Europe. Even our Japanese Air Source Heat Pump was manufactured in Scotland!”
With planning consent granted it was left to MBC to install the Passiv standard foundations and slab before moving on to erect the carefully designed frame for the house which was ultimately clad in clay tiles.
“The MBC team for both the foundation build up and the frame erection were brilliant. The team that you assemble for a self build is so critical to the success of a self build project and bearing in mind MBC were pretty much the first on site, they set the tone for a “can do” approach to the project from the outset,” he continued.
The key design element of the house is a huge expanse of triple glazed sliding doors weighing in at a hefty 2½ tonnes in total. This feature is the gateway to light and sunshine throughout the year. Solar gain has been given real thought by the architect. During the winter, low sunlight manages to encroach under the canopy all the way through to the skirting board line at the rear of the house, while during the Summer the sun rises to such an extent that the canopy provides shade and prevents undue solar gain and consequent overheating of the stunning internal spaces of the house.
The self build that Philip and Jan built 15 years ago was, for its time, thermally efficient, but things have moved on hugely. For this build Philip decided that the aims and standards of a Passive solution were desirable but not necessary to the point of Passiv Certification.
Passive build standards demand an energy use of 15Kw/hour per m2 per year and “Wayside” delivers an impressive 10Kw/hour per m2 per year – easily surpassing the Passiv standard. The average house in the UK operates at about 120Kw/hour per m2. A 200m house therefore soaks up an annual 24,000 Kw/hours.
“It’s against that background that we were pleasantly surprised to achieve a consumption of 1,800 Kw/hours for heating and 1,200 Kw/hours for hot water for a 300m2 house – the figures speak for themselves,” says Philip.