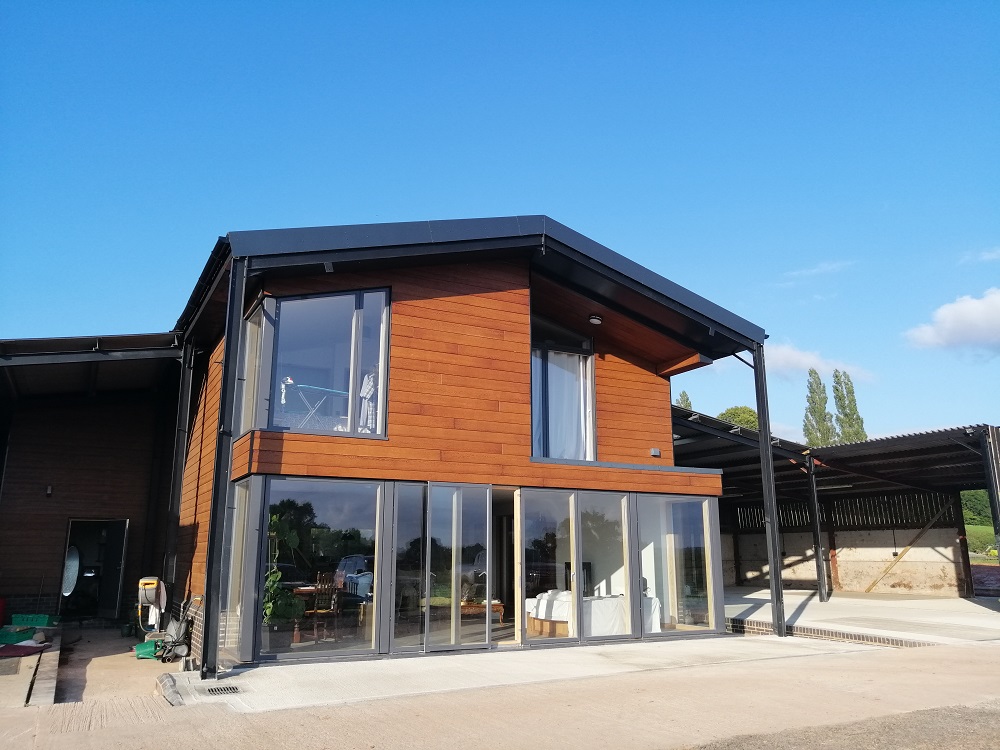
Project Name: Leadon Dale
Company: Frame Technologies
Sector: Self Build
Technology: TechVantage™ S
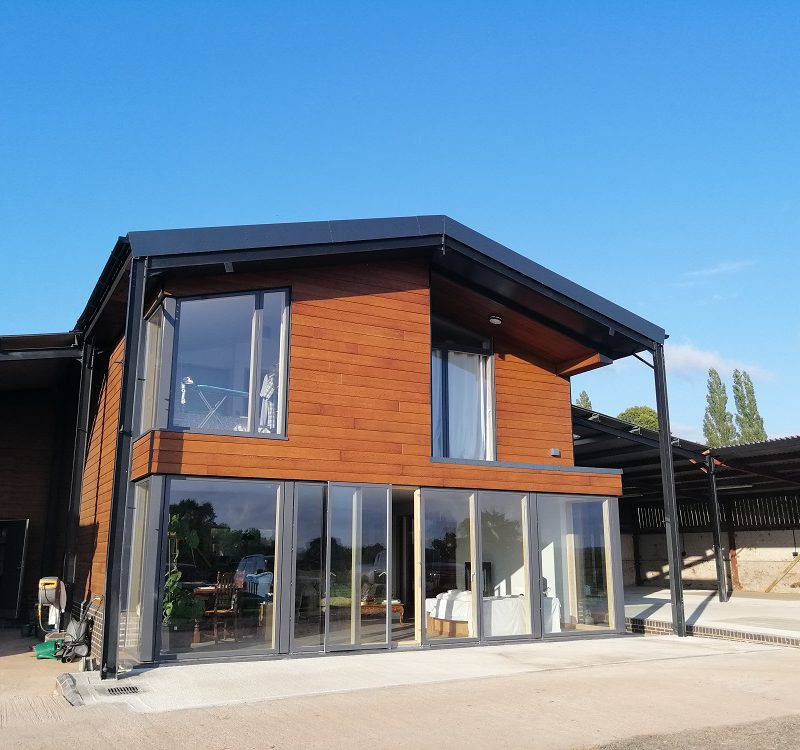
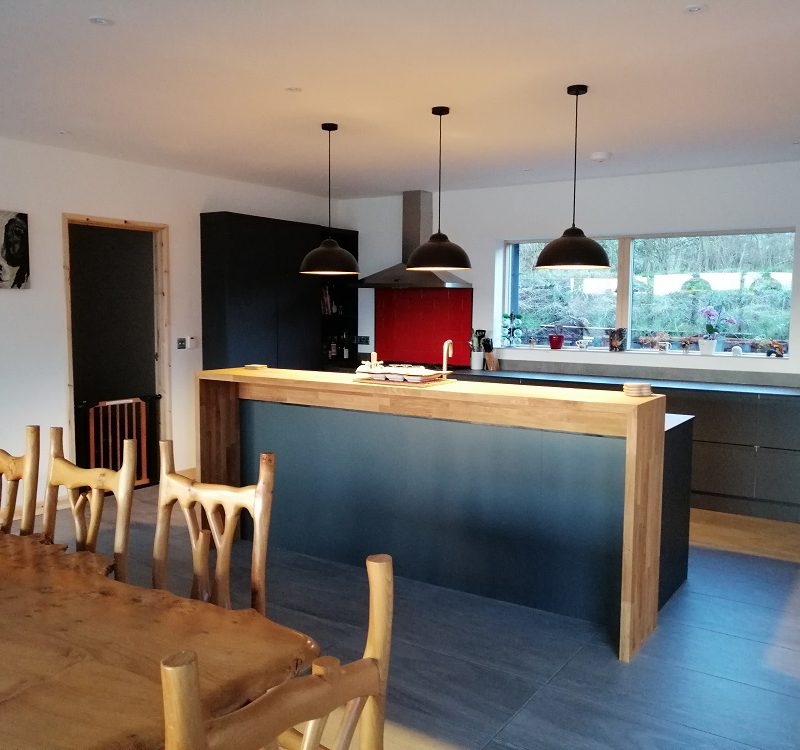

Overview:
Nestled in an eight-acre field for grazing livestock, Frame Technologies created an energy-efficient timber system to convert a steel-framed agricultural barn and concrete yard into a sensitively integrated residential dwelling. Idyllically located in Herefordshire’s natural landscapes, the conversion offers a new home for a countryside family. Following the completion of the Leadon Dale barn conversion, the homeowners recommended Frame Technologies to a colleague who visited the site. As a result, they also commissioned Frame Technologies to complete their change of use barn conversion.
The Challenge:
Initially, the homeowners were concerned because planning permission for an onsite residence was unlikely. However, with an application under Permitted Development Part Q for change of use on an existing agricultural building to one residential dwelling house, planning permission was granted.
Adopting a fabric first approach to ensure optimum energy efficiency, Frame Technologies created a unique timber solution to overcome challenges that the existing barn presented: the original steel framework needed to remain in situ and the original building dimensions could not be increased. Embracing the brief’s requirements, Frame Technologies integrated architectural drawings and additional client design requests to create a barn conversion that blends into its natural surroundings, retaining its agricultural theme using an innovative timber system and cement timber-effect cladding boards.
Achieving The Optimum Performance:
Frame Technologies created a TechVantage™ S system to convert the barn – historically used for winter housing of beef cattle and hay storage – into a homely residential dwelling. The TechVantage™ S system comprises a 140mm panel with glass mineral wool insulation that is tightly packed between a sheathing board and a wood fibre board. Inside the panel, a 25mm service batten is nailed to the OSB. The system uses a breathable wall principle with natural insulation, delivering a wall U-value of 0.14 W/m2K. The system’s excellent thermal properties are combined with the impressive solar gain from the south-facing glazing in this contemporary self-build conversion.
To reduce cold bridging, the wall is sheathed with 20mm wood fibre board, which is fixed to a 140mm timber stud with full fill insulation. A 9mm OSB is fitted internally with a site-fitted PIR insulation, including tapered joints, a 25 x 50mm service batten and 15mm plasterboard. The floors use 254mm top hung metal web joists, as opposed to traditional ring beams, to reduce shrinkage and improve thermal performance through the floor zone.
Frame Technologies achieved optimal airtightness through a timber system that includes membranes and tapes for sealing joints or apertures around building services, airtightness detailing in critical areas such as intermediate floor to external wall panels, battens to form service zones and reduce the need for penetration through the barriers and OSB sheathing on internal faces of external walls that were then taped to provide excellent results.
Offsite Manufactured Timber Frame:
Following a site measure and survey, it became apparent that the original slanted steel framework was in twist. On consultation with Frame Technologies, the client up righted the building based on our structural details. The next challenge was to erect the wall panels and integrate the existing steel trusses of the old building with the roof zone of the new building. Frame Technologies achieved this using an engineered rafter, sheathing and roof sheets that match the existing design.
As the UK’s fastest growing construction method, timber frame is the popular route to green, environmentally-conscious structures. Offsite manufactured timber frame is 30% faster to construct than traditional building methods that use brick and block, concrete, steel and aluminium – Frame Technologies were able to make the structure for this home weather-tight within days. With predictable project planning, efficiency was maximised and onsite risks were minimised. The self build was also quick to construct as internal works could run parallel to external finishes. Not only is the timber system environmentally friendly, recyclable and waste efficient, it is also lightweight, requiring only cost-effective, simple foundations. Fabricated in our precision-controlled factory in Presteigne, Frame Technologies were able to keep construction costs, delays and onsite labour to a minimum during this project.
Frame Technologies carefully considered the home entrance as the client’s farming and agricultural lifestyle requires a high level of ‘clean-up’. The new timber dwelling incorporates undercover car parking for protected access to the barn conversion, as well as a downstairs shower room at the immediate entrance. To improve storage and finalise the newly converted barn, Frame Technologies created two custom loft spaces in the roof voids to the left and right of the main living area.
The clients were delighted with the outcome:
“When we were obtaining quotations for the timber frame, the majority of companies we approached were put off by the requirement for the steel-framed building to remain in situ. In contrast, Frame Technologies welcomed the challenge. They were easy to talk to and communicated regularly with project updates. Not only did they assist with sourcing suppliers and keep to all deadlines, they also sourced additional installation and returned to the site following timber frame erection to install the external cladding system.”