Structural timber guides the way on the road to net zero
27/06/2023
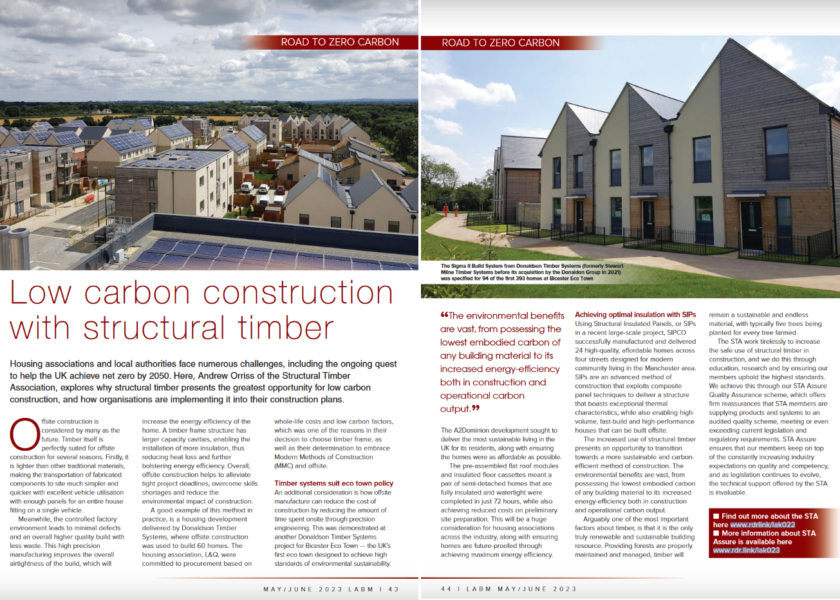
Housing associations and local authorities are facing numerous obstacles at the moment, including the ongoing quest to help the UK achieve net zero by 2050. With this in mind, it has been encouraging to see more organisations using structural timber in their developments to help solve this industry issue. Here, Andrew Orriss of the Structural Timber Association, explores why structural timber presents the greatest opportunity for low carbon construction, and how companies are implementing it into their construction plans.
Offsite construction is considered by many as the future. Timber itself is perfectly suited for offsite construction for several reasons. Firstly, it is lighter than other traditional materials, making the transportation of fabricated components to site much simpler and quicker with excellent vehicle utilisation with enough panels for an entire house fitting on a single vehicle.
Meanwhile, the controlled factory environment leads to minimal defects and an overall higher quality build with less waste. This high precision manufacturing improves the overall airtightness of the build which will increase the energy efficiency of the home. A timber frame structure has larger capacity cavities, enabling the installation of more insulation, thus reducing heat loss and further bolstering energy efficiency. Overall, offsite construction helps to alleviate tight project deadlines, overcome skills shortages and reduce the environmental impact of construction.
A good example of this method in practice, is a housing development delivered by Donaldson Timber Systems, where offsite construction was used to build 60 homes. The client, L&Q, were committed to procurement based on whole-life costs and low carbon factors, which was one of the reasons in their decision to choose timber frame, as well as their determination to embrace Modern Methods of Construction (MMC) and offsite.
Timber systems suit eco town policy
An additional consideration is how offsite manufacture can reduce the cost of construction by reducing the amount of time spent onsite through precision engineering. This was demonstrated at another Donaldson Timber Systems project for Bicester Eco Town – the UK’s first eco town designed to achieve high standards of environmental sustainability. The A2Dominion development sought to deliver the most sustainable living in the UK for its residents, along with ensuring the homes were as affordable as possible. The pre-assembled flat roof modules and insulated floor cassettes meant a pair of semi-detached homes, that are fully insulated and watertight were completed in just 72 hours, while also achieving reduced costs on preliminary site preparation. This will be a huge consideration for housing associations across the industry, along with ensuring homes are future-proofed through achieving maximum energy efficiency.
Achieving optimal insulation with SIPs
Using Structural Insulated Panels, or SIPs in a recent large-scale project, SIPCO successfully manufactured and delivered twenty-four high-quality, affordable homes across four streets designed for modern community living in the Manchester area. SIPs are an advanced method of construction that exploits composite panel techniques to deliver a structure that boasts exceptional thermal characteristics, while also enabling high-volume, fast-build and high-performance houses that can be built offsite.
The increased use of structural timber presents an opportunity to transition towards a more sustainable and carbon-efficient method of construction. The environmental benefits are vast, from possessing the lowest embodied carbon of any building material to its increased energy-efficiency both in construction and operational carbon output. Arguably one of the most important factors about timber, is that it is the only truly renewable and sustainable building resource. Providing forests are properly maintained and managed, timber will remain a sustainable and endless material, with typically five trees being planted for every tree farmed.
The STA work tirelessly to increase the safe use of structural timber in construction, and we do this through education, research and by ensuring our members uphold the highest standards. We achieve this through our STA Assure Quality Assurance scheme, which offers firm reassurances that STA members are supplying products and systems to an audited quality scheme, meeting or even exceeding current legislation and regulatory requirements. STA Assure ensures that our members keep on top of the constantly increasing industry expectations on quality and competency, and as legislation continues to evolve, the technical support offered by the STA is invaluable.
Read full article here