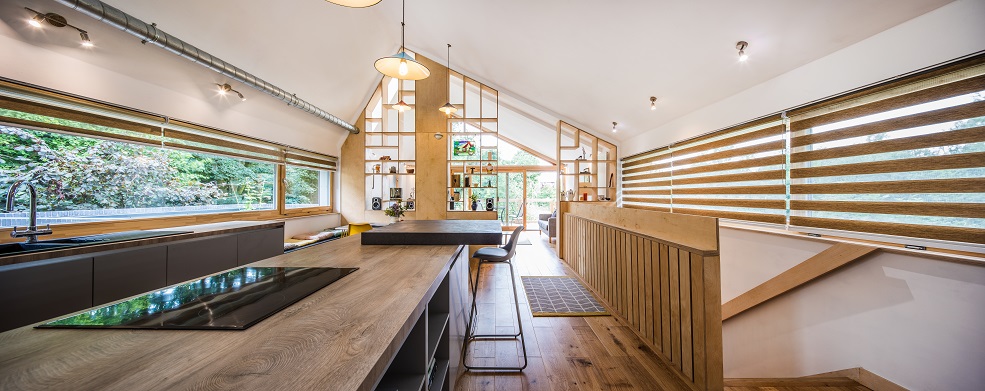
Project Name: The Hen House
Company: Frame Technologies
Sector: Self Build
Technology: TechVantage™ E
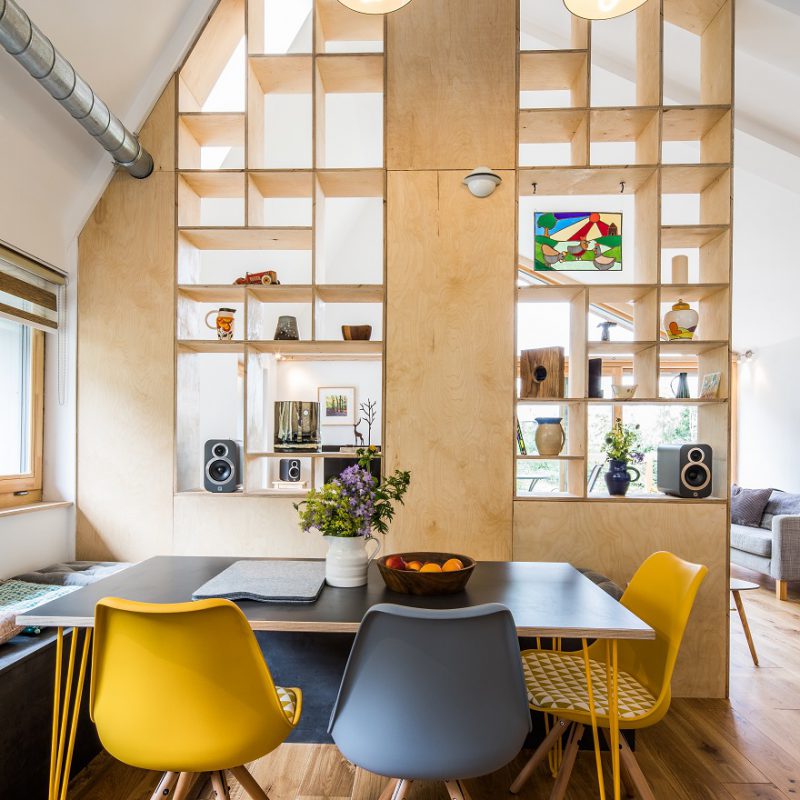
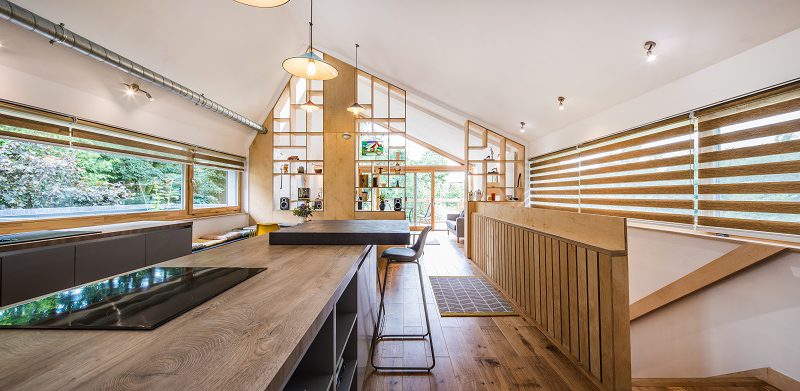
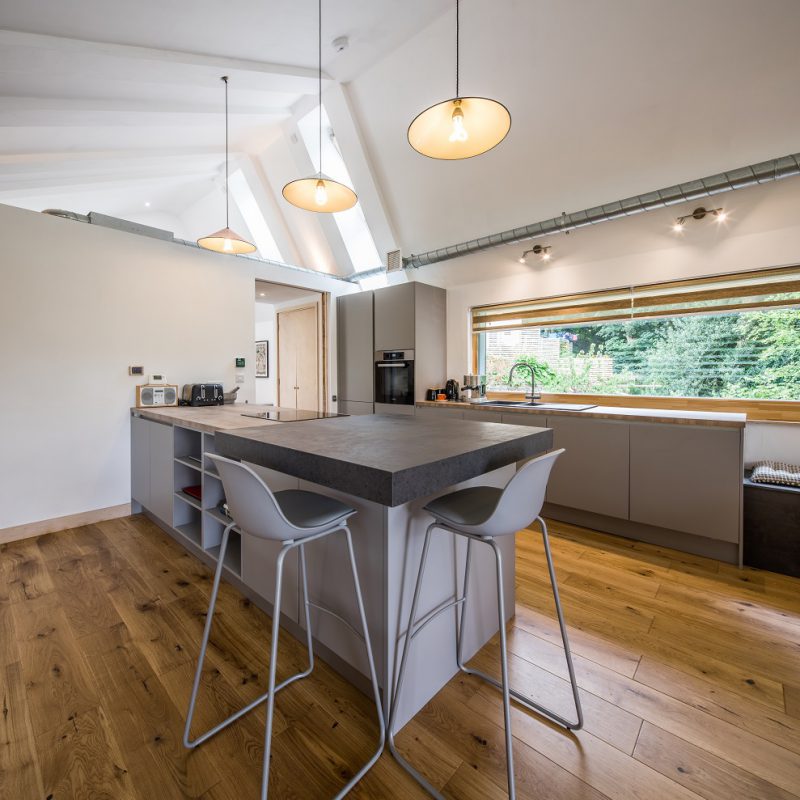
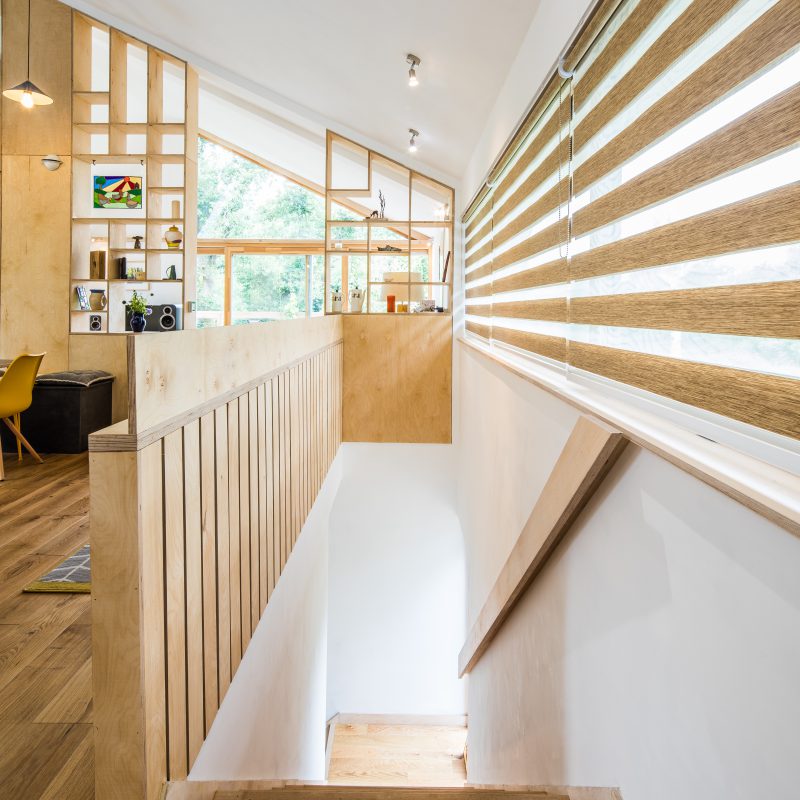
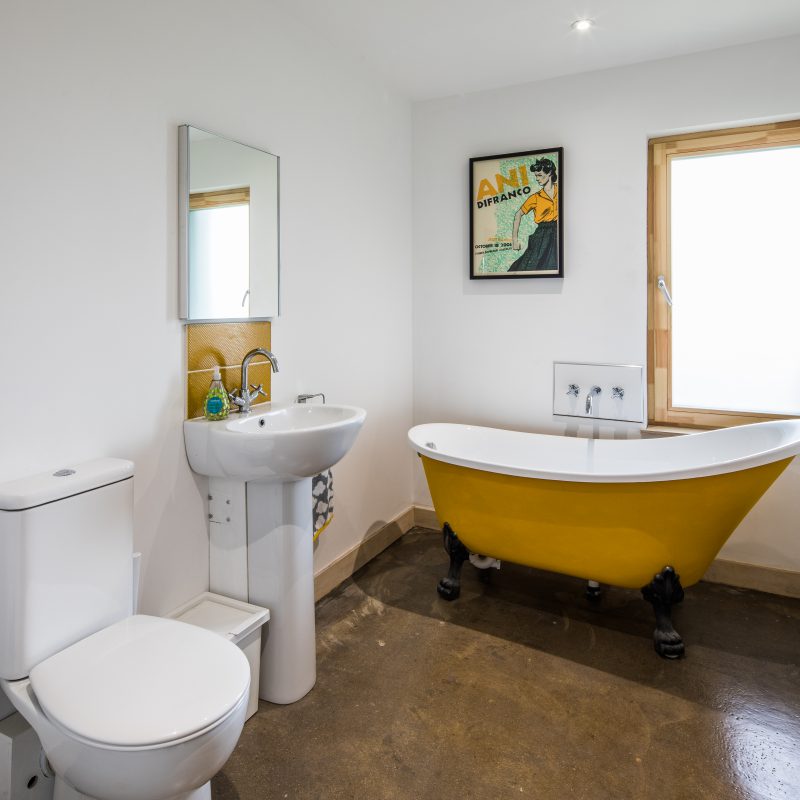
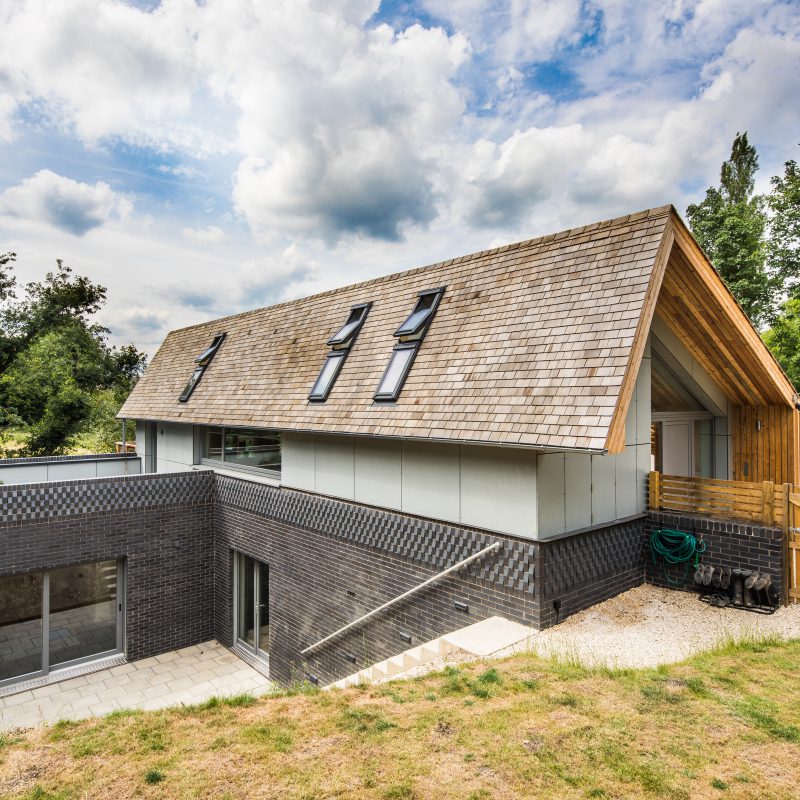
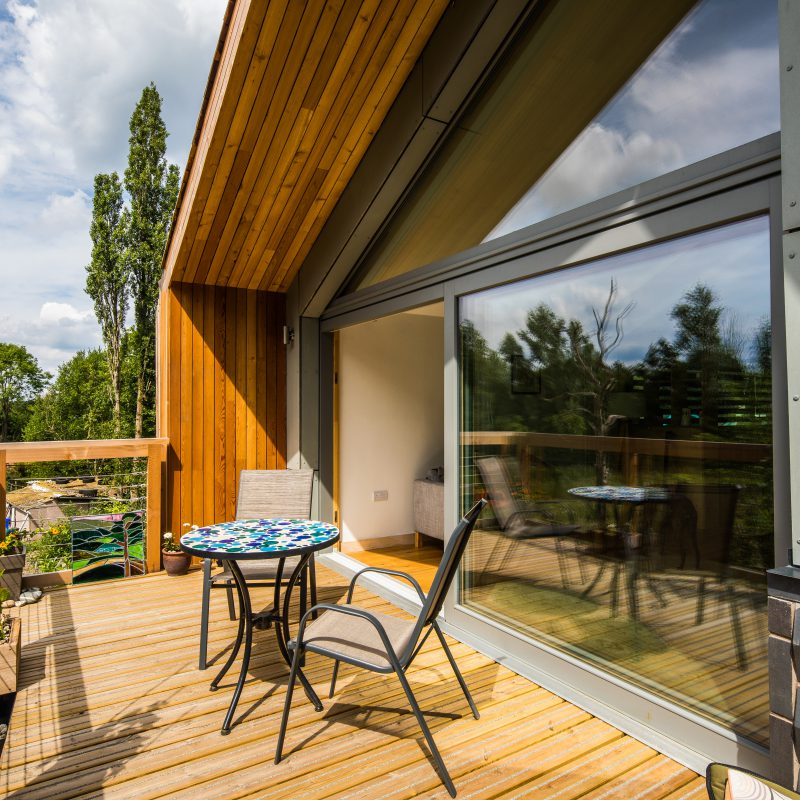
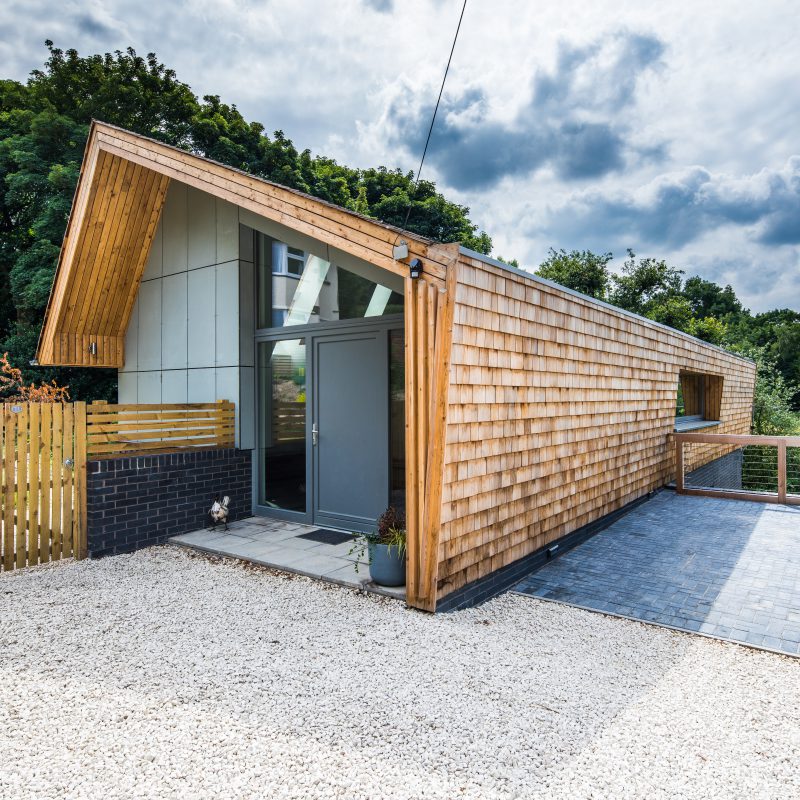
Overview:
Frame Technologies have worked on a variety of energy-efficient self build projects throughout the UK. Every project is bespoke and designed to meet individual requirements. Even with this extensive experience, The Hen House presented some major challenges. To maximise the potential of offsite-manufactured timber technology, Frame Technologies prefer to get involved in the early design stages. On this occasion, our specialist services were called upon when the project could not be achieved within budget using the traditional building methods proposed. The team at Frame Technologies reviewed the building principles and proposed a hybrid engineered solution that could be delivered within budget.
The Challenge:
The site is a tough one – a steep, wooded plot with a gradient of circa 50 degrees. A large proportion of the site area is covered by a Tree Protection Order. Paul Testa Architecture decided to position the foundations on the lower portion of the site in the spot where the hens used to live, hence the project name – The Hen House. From the road, this development appears to be single storey. However, due to be being built on a steep incline, only the true scale of the project can be seen from the rear.
Meeting The Brief:
The clients brought Passivhaus methodology into the process, but they were not initially committed to the standard itself. Having visited some completed projects on Passivhaus open days, this changed and a fully functioning Passivhaus became our target.
Offsite Approach:
A true offsite-manufactured timber system was not the initial specified structural solution. However, it soon became apparent that only by using modern methods of offsite construction could this self build scheme be delivered.
Frame Technologies designed, manufactured and installed all the structural timber elements. The structural system was designed to spread the load more evenly, in a uniformed way. This was not only more efficient but eliminated big point loads with a fully vaulted spread. This offered savings on groundworks. It was calculated that the reduction in weight achieved by using this system delivered £10,000 of cost savings in foundations to support the robust, yet lighter weight superstructure. Frame Technologies also helped with guidance on the building fabric performance and the sourcing of sustainable materials to achieve an energy-efficient home built to Passivhaus Principles.
Tech-Vantage E™, a 140 mm panel containing Rigid Urethane Insulation, was the preferred timber frame system to not only deliver the project but to achieve the desired performance standards. Manufactured in Frame Technologies’ factory, Tech-Vantage E™ is a closed panel solution which achieves exceptional U-values through high-performance thermal insulation.
Partnership Approach:
Unlike many other structural timber companies, Frame Technologies take control of the entire process. By working in collaboration with Paul Testa Architecture, the engineers from Jon Carr Structural Design and M&E consultants, MVHR, we designed and fully engineered our TechVantage™ E system for the project. We manufactured all the structural timber elements offsite in our own factory and finally delivered the frame to site and installed the superstructure.
This end-to-end service provides consistency throughout the process. By using the advanced TechVantage™ E system, U-values are significantly easier to predict. Airtightness must also be factored into the performance equation. Good airtightness can be achieved with simple detailing.
Paul Testa said of the collaboration: “The Hen House site is complex and constrained with an innovative design that needed to accommodate tricky levels and access. Working with Frame Technologies allowed us to access great expertise in developing a timber frame solution that was structurally appropriate and quick to erect. The project wasn’t without its challenges and Frame Technologies were flexible and professional in their approach to helping us to deliver a fantastic home for our clients. Simon is clearly very knowledgeable and offered us great support throughout.”
Achieving The Optimum Performance:
Frame Technologies’ developments meet and can even surpass current regulation requirements with airtightness less than 1m3/h/m2. Using offsite prefabricated structural timber provides faster speed of build than traditional methods of construction – typically 30% quicker. Once onsite, our TechVantage™ E system took just eight days to erect. Timber frame construction is not weather-dependent due to most of the work being completed in the factory, which makes project planning more predictable and reduces risk of setbacks. The follow-on trades started work much earlier, which meant that the build could be finished way ahead of the predicted schedule for a traditionally constructed home.
Frame Technologies’ panellised the lower floor – metal web joists were used to create a timber deck which runs across the full storey, and a steel ‘A Frame’ was incorporated into the design to form the offset ridge of the roof to create a clear internal ceiling with no tie wires or beams. Using timber allows for more accurate budgeting, which is so important when self-building. The finished building is better insulated and thermally efficient, with a lifetime of lower costs and energy bills, delivering a true Fabric First ‘fit and forget’ ethos.
System specification and early involvement is key to success when creating an energy-efficient, sustainable home. One of the main decisions that the architects faced on this project was the choice between traditional and true modern methods of offsite construction. Initially, traditional methods were considered but it was decided that only a high-performance advanced timber structure could deliver the project and achieve the performance specified in the brief.
Understanding and addressing the gap between projected and actual performance is an industry-wide challenge and there are multiple house-building delivery routes, which makes mapping the process a complex task. Our TechVantage™ E system overcomes this issue, as performance is tested and more predictable. The 140 mm closed panel system contains Rigid Urethane Insulation and is available in a variety of depths to meet specific U-value requirements from 0.09 W/m2K to 0.23 W/m2K. The closed panel has a 9 mm OSB outer sheathing and either a Vapour Control Layer or a 20 mm or up to 110 mm layer of extra insulation on the inside of the panel with taped joints – to meet varying U-Value objectives. There are service zones between the insulation layers.
The Fabric First Approach, adopted by Frame Technologies, creates a high-performance, thermally efficient building envelope that can achieve up to Passivhaus Standards without relying on expensive energy-saving bolt-on technologies, such as solar panels. At Frame Technologies, our mission is to add value to drive down overall project costs throughout the build and beyond to create a highly energy-efficient home – reducing ongoing costs for the lifetime of the building.