Mapping the future of timber in construction
06/06/2024
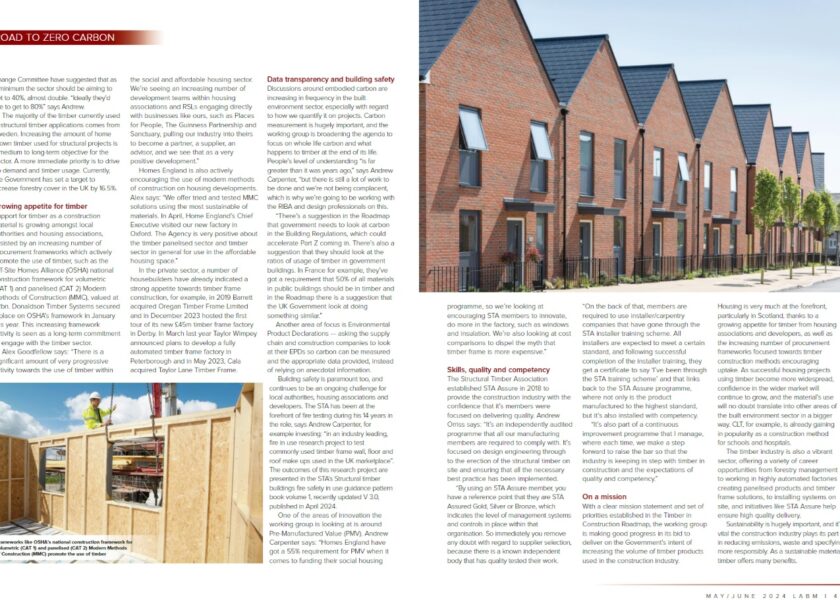
LABM speaks to Andrew Carpenter, Chief Executive of the Structural Timber Association, Andrew Orriss, Chief Operating Officer at the STA and Alex Goodfellow, CEO of Donaldson Offsite and Chairperson of the Confederation of Timber Industries, about why the introduction of the Timber in Construction (TiC) Policy Roadmap is so important and its impact on the construction industry.
In the UK, recognising the impact of the built environment on emissions targets, the Government instigated a new working group with a mission to increase the amount of sustainable timber used in construction in December 2021. Set up in the wake of COP26, the group’s work is the genesis behind the creation of the Timber in Construction (TiC) Policy Roadmap, launched in December last year. The working group consists of a cross section of government departments
Andrew Carpenter says: “The Government recognised that if it’s going to meet its net zero target by 2050, and with construction responsible for 40% of all emissions, they had to consider the behaviour of the UK construction sector, and inevitably, the materials we use. Concrete and steel for example are two of the biggest emitters of embodied carbon during their manufacture, whereas timber has the opposite effect, so looking at building materials was an important factor.”
Andrew Carpenter from the STA, David Hopkins from Timber Development UK (TDUK) and Andy Leitch for the Confederation of Forest Industries (UK) (Confor) represent the timber sector in the working group.
Andrew Carpenter says: “Between the three of us, we cover the whole timber supply chain, and along with another dozen industry experts on the working group, including members from the RIBA, HBF and HSC, identified seven areas that we had to work on.”
Roadmap priorities
Promoting the wider use of timber as a construction material, increasing the sustainable supply of timber, growing skills, capacity and competency, improving data, particularly around whole life carbon, tackling fire safety and durability concerns, increasing collaboration and confidence with insurers, lenders and warranty providers, and promoting innovation in timber construction systems make up the seven key areas.
The market share for timber frame in housing across the UK is currently 23%. The Environmental Audit Committee and Climate Change Committee have suggested that as a minimum the sector should be aiming to get to 40%, almost double. “Ideally they’d like to get to 80%” says Andrew.
The majority of the timber currently used in structural timber applications comes from Sweden. Increasing the amount of home grown timber used for structural projects is a medium to long-term objective for the sector. A more immediate priority is drive up demand and timber usage. Currently, the Government has set a target to increase forestry cover in the UK by 16.5%.
Growing appetite for timber
Support for timber as a construction material is growing amongst local authorities and housing associations, assisted by an increasing number of procurement frameworks which actively promote the use of timber, such as the Off-Site Homes Alliance (OSHA) national construction framework for volumetric (CAT 1) and panelised (CAT 2) Modern Methods of Construction (MMC), valued at £2bn. Donaldson Timber Systems secured a place on OSHA’s framework in January this year. This increasing framework activity is seen as a long-term commitment to engage with the timber sector.
Alex Goodfellow says: ”There is a significant amount of very progressive activity towards the use of timber within the social and affordable housing sector. We’re seeing an increasing number of development teams within housing associations and RSLs engaging directly with businesses like ours, such as Places for People, The Guinness Partnership and Sanctuary, pulling our industry into theirs to become a partner, a supplier, an advisor, and we see that as a very positive development.”
Homes England is also actively encouraging the use of modern methods of construction on housing developments. Alex says: “We offer tried and tested MMC solutions using the most sustainable of materials. In April, Home England’s Chief Executive visited our new factory in Oxford. The Agency is very positive about the timber panelised sector and timber sector in general for use in the affordable housing space.”
In the private sector, a number of housebuilders have already indicated a strong appetite towards timber frame construction, for example, in 2019 Barrett acquired Oregan Timber Frame Limited and in December 2023 hosted the first tour of its new £45m timber frame factory in Derby. In March last year Taylor Wimpey announced plans to develop a fully automated timber frame factory in Peterborough and in May 2023, Cala acquired Taylor Lane Timber Frame.
Data transparency and building safety
Discussions around embodied carbon are increasing in frequency in the built environment sector, especially with regard to how we quantify it on projects. Carbon measurement is hugely important, and the working group is broadening the agenda to focus on whole life carbon and what happens to timber at the end of its life. People’s level of understanding “is far greater than it was years ago,” says Andrew Carpenter, “but there is still a lot of work to be done and we’re not being complacent, which is why we’re going to be working with the RIBA and design professionals on this.
“There’s a suggestion in the Roadmap that government needs to look at carbon in the Building Regulations, which could accelerate Part Z coming in. There’s also a suggestion that they should look at the ratios of usage of timber in government buildings. In France for example, they’ve got a requirement that 50% of all materials in public buildings should be in timber and in the Roadmap there is a suggestion that the UK Government look at doing something similar.”
Another area of focus is Environmental Product Declarations — asking the supply chain and construction companies to look at their EPDs so carbon can be measured and the appropriate data provided, instead of relying on anecdotal information.
Building safety is paramount too, and continues to be an ongoing challenge for local authorities, housing associations and developers. The STA has been at the forefront of fire testing during his 14 years in the role,says Andrew Carpenter, for example investing: “in an industry leading, fire in use research project to test commonly used timber frame wall, floor and roof make ups used in the UK marketplace”. The outcomes of this research project are presented in the STA’s Structural timber buildings fire safety in use guidance pattern book volume 1, recently updated V 3.0, published in April 2024.
One of the areas of innovation the working group is looking at is around Pre Manufactured Value (PMV). Andrew Carpenter says: “Homes England have got a 55% requirement for PMV when it comes to funding their social housing programme, so we’re looking at encouraging STA members to innovate, do more in the factory, such as windows and insulation. We’re also looking at cost comparisons to dispel the myth that timber frame is more expensive.”
Skills, quality and competency
The Structural Timber Association established STA Assure in 2017 to provide the construction industry with the confidence that it’s members were focused on delivering quality. Andrew Orriss says: “It’s an independently audited programme that all our manufacturing members are required to comply with. It’s focused on design engineering through to the erection of the structural timber on site and ensuring that all the necessary best practice has been implemented. By using an STA Assure member, you have a reference point that they are STA Assured Gold, Silver or Bronze, which indicates the level of management systems and controls in place within that organisation. So immediately you remove any doubt with regard to supplier selection, because there is a known independent body that has quality tested their work.
“On the back of that, members are required to use installer/carpentry companies that have gone through the STA installer training scheme. All installers are expected to meet a certain standard, and following successful completion of the training, they get a certificate to say ‘I’ve been through the STA installer training scheme’ and that links back to the STA Assure programme, where not only is the product manufactured to the highest standard, but it’s also installed with competency.
“It’s also part of a continuous improvement programme that I manage, where each time, we make a step forward to raise the bar so that the industry is keeping in step with timber in construction and the expectations of quality and competency.”
On a mission
With a clear mission statement and set of priorities established in the Timber in Construction Roadmap, the working group is making good progress in its bid to deliver on the Government’s intent of increasing the volume of timber products used in the construction industry.
Housing is very much at the forefront, particularly in Scotland, thanks to a growing appetite for timber from housing associations and developers, as well as the increasing number of procurement frameworks focused towards timber construction methods encouraging uptake. As successful housing projects using timber become more widespread, confidence in the wider market will continue to grow, and the material’s use will no doubt translate into other areas of the built environment sector in a bigger way. CLT, for example, is already gaining in popularity as a construction method in schools and hospitals.
The timber industry is also a vibrant sector, offering a variety of career opportunities from forestry management to working in highly automated factories creating panelised products and timber frame solutions, to installing systems on site, and initiatives like STA Assure help ensure high quality delivery.
Sustainability is hugely important, and it’s vital the construction industry plays its part in reducing emissions, waste and specifying more responsibly. As a sustainable material, timber offers many benefits.